A Beginner’s Guide to Foundry Equipment and Its Uses
Explore the essential equipment and technologies powering modern foundries. Learn about advanced casting machines, safety features, and innovative solutions for efficient metal casting operations.
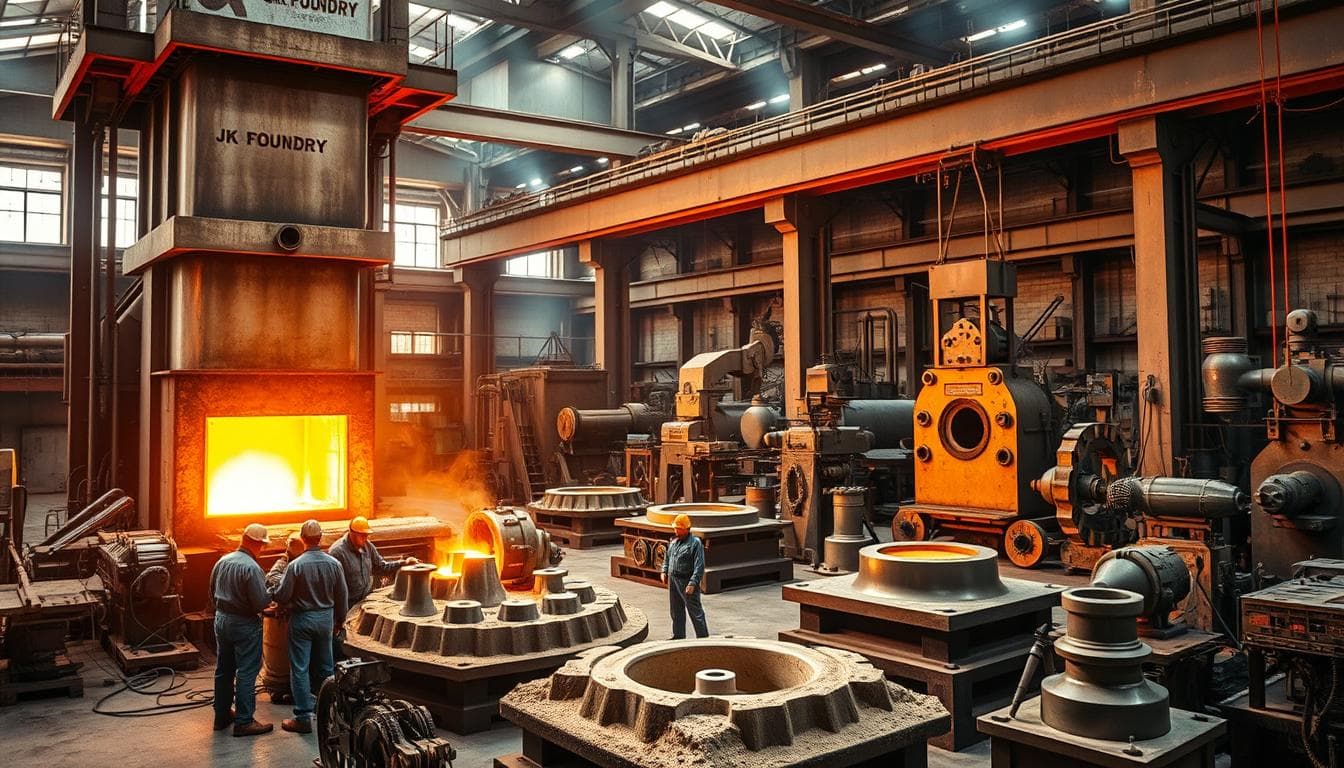
Ever wondered how metal turns into precise parts? The world of foundry equipment is full of secrets that power modern manufacturing. It's fascinating to see how it works.
Foundry equipment is key to metal casting. These advanced machines and tools help make complex metal parts with great precision and speed. They're used for everything from car parts to huge industrial machines.
Learning about foundry equipment is more than just tech talk. It's about understanding the detailed process that turns raw materials into solutions that drive innovation in many fields.
Key Takeaways
- Foundry equipment is essential for metal casting processes
- Casting machines enable precise manufacturing of metal components
- Modern foundry technology supports diverse industrial applications
- Equipment selection impacts production efficiency and quality
- Continuous technological advancements improve casting techniques
Essential Foundry Equipment for Modern Casting Operations
Modern foundries use advanced tools to turn raw materials into precise metal parts. Choosing the right equipment is key to successful casting. It must meet the specific needs of each manufacturing task.
Advanced Casting Machines for Precision Manufacturing
Casting machines are vital in metal making. They come in different types for various industrial needs:
- Gravity die casting machines for even metal spread
- High-pressure die casting machines for detailed shapes
- Low-pressure casting machines for big car parts
Melting Furnace Technologies: A Comparative Analysis
Choosing the right melting furnaces is vital for efficient metal making. Two main technologies stand out:
Induction Furnaces
- Accurate temperature control
- Clean melting area
- More energy efficient
Cupola Furnaces
- Lower start-up costs
- Good for big production
- Classic metal melting way
Prioritizing Safety in Foundry Equipment
Today's foundry gear has top-notch safety features. These protect workers and keep operations running smoothly. Key safety parts include thermal sensors, auto-shutoff, and safety barriers.
Safety isn't an option in foundry operations—it's a fundamental requirement for sustainable manufacturing.
Understanding Molding and Core Making Systems
Foundries use advanced molding equipment to make precise metal castings. Core shooters are key in this process. They help create detailed internal shapes with great accuracy.
Modern Molding Tools
Modern molding tools have changed how we cast metal parts. These systems come in different types:
- Manual molding systems for small-scale production
- Semi-automated molding equipment for medium-volume manufacturing
- Fully automated core shooters for large-scale industrial applications
Core shooters are special machines. They turn loose sand into exact mold cores. They use compressed air to pack sand into detailed shapes, ensuring top-notch accuracy and finish.
Precision in molding equipment determines the quality of the final cast product.
Equipment Selection Factors
Choosing the right molding equipment is important. It depends on several factors:
- Production volume requirements
- Complexity of casting design
- Material specifications
- Budget constraints
Investing in advanced core shooters and molding equipment can significantly enhance manufacturing efficiency and product quality.
Sand Preparation and Material Handling Equipment
Foundries need advanced sand preparation systems for top-notch castings. These systems are key to keeping sand quality and consistency high.
Good material handling starts with knowing how to manage sand well. Foundries must have strong plans to control sand and improve casting quality.
Sand Testing and Quality Control Methods
Quality control in sand prep includes several key steps:
- Moisture content analysis
- Grain size distribution evaluation
- Permeability testing
- Compactability assessments
Automated Material Transport Systems
Modern shake-out systems have changed material handling with new tech. They:
- Lower the need for manual labor
- Make operations more efficient
- Lessen the risk of material contamination
- Speed up production
Reclamation Equipment and Sustainability
Today's sand prep systems use advanced reclamation tech. Sustainable foundry practices aim to recycle and reuse sand. This cuts down on environmental harm while keeping casting quality high.
Innovative foundry equipment turns material handling into a strategic advantage.
Heat Treatment and Post-Processing Solutions
In metal casting, heat treatment ovens are key. They turn raw castings into top-notch parts. These ovens control temperature and cooling to boost metal part strength.
Heat Treatment Process
The heat treatment process includes several important steps:
- Normalizing to refine grain structure
- Annealing to reduce internal stress
- Hardening to increase strength
- Tempering to improve ductility
Fettling and Finishing
Fettling machines help by getting castings ready for use. They remove extra material, smooth surfaces, and check dimensions. Skilled workers use these machines to fix imperfections, making the product look great.
Precision in heat treatment and post-processing can dramatically improve the quality and performance of metal castings.
Top foundries use the latest heat treatment ovens and fettling machines. They learn these techniques to make better products. This way, they improve quality, cut down on waste, and meet customer needs.
Conclusion
Finding the right foundry equipment is key. It needs smart thinking and always learning. The right tools and equipment can make casting better and more efficient in India.
Quality control starts with knowing advanced machines and strict testing. Today's foundry workers must use the latest gear. This gear helps make products better and cuts down on waste.
New technologies are changing how we make things. New foundry equipment can make production better. It's important for engineers and managers to keep learning and using the latest tech.
Choosing the best equipment is the first step to making things better. By focusing on precision, safety, and new tech, foundries can make top-quality products. This helps them stand out in India's fast-changing industry.
Ready to Transform Your Manufacturing?
Discover how our advanced steel casting technology can revolutionize your manufacturing process.
Contact Us Today