Step-by-Step Guide to Metal Casting: From Molding to Finishing
Explore the comprehensive process of metal casting, from initial molding to final finishing. Learn about different casting techniques, safety protocols, and quality control measures in modern foundries.
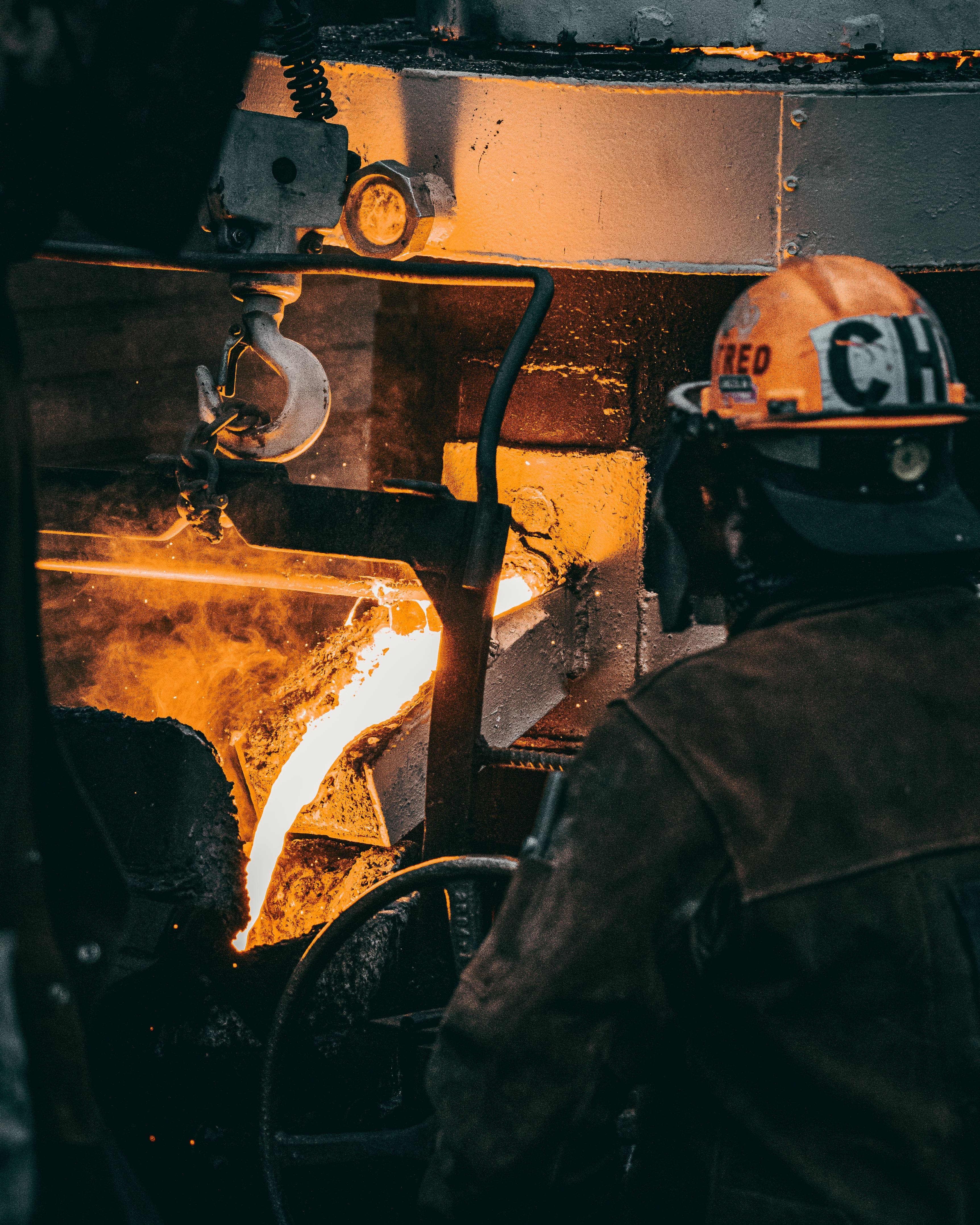
Metal casting is a key method in making parts for many industries. It turns raw materials into precise components. This process involves pouring molten metal into molds, making complex parts with great accuracy.
In fields like car making and space tech, metal casting is vital. Experts use special techniques to turn liquid metal into solid shapes. They focus on making sure the parts are strong and precise.
This guide will dive into the world of metal casting. It will cover techniques, tools, and best practices. This helps engineers and makers create top-notch metal parts efficiently.
Key Takeaways
- Metal casting enables complex component manufacturing
- Precise mold design is crucial for successful casting
- Different metals require specialized casting techniques
- Safety protocols are essential in metal casting operations
- Quality control determines final product performance
Understanding the Metal Casting Process
The metal casting process is key in making things. It turns molten metal into exact shapes and parts. This old method is still important today in many fields, like cars and planes.
At its heart, metal casting uses basic ideas. These ideas help make complex metal parts with great accuracy.
Basic Principles and Terminology
To get metal casting, you need to know some important words:
- Molten Metal: Heated metal in liquid state ready for casting
- Pattern: Replica of the desired final product used to create mold cavity
- Mold: Container where molten metal is poured and solidified
- Core: Internal section that creates hollow spaces in the casting
Types of Metal Suitable for Casting
Various metals are good for casting because of their special qualities:
- Aluminum: Lightweight, corrosion-resistant
- Bronze: Strong, wear-resistant
- Steel: High strength, versatile applications
- Iron: Durable, cost-effective
Essential Safety Protocols
Safety is very important in metal casting. Workers must wear protective gear like heat-resistant clothes and face shields. They also need insulated gloves. It's important to have good air flow and know how to handle hot metal to avoid accidents.
Safety isn't just a procedure – it's a commitment to protecting skilled workers and maintaining operational excellence.
Essential Tools and Equipment for Metal Casting
Metal casting needs special tools and equipment to shape molten metal. Professional foundries use advanced machinery for various casting methods. This includes die casting and permanent mold casting.
Core Equipment
The main tools for metal casting are:
- High-temperature crucible furnaces for melting metals
- Precision molds for shaping molten material
- Pouring tools with heat-resistant handles
- Temperature measurement instruments
- Protective safety gear
Modern Technology Integration
Today, foundries use computer-controlled equipment for better accuracy. They use advanced thermal imaging cameras and digital temperature systems. These tools help technicians keep the casting conditions perfect for different metals.
Designing and Creating Casting Patterns
Creating patterns is key in metal casting. It affects the quality and accuracy of the final product. Patterns are like blueprints for metal parts, whether using investment or lost foam casting.
Pattern Materials and Selection
Choosing the right pattern material is very important. Each casting method needs specific materials:
- Wood for traditional sand casting
- Polystyrene foam for lost foam casting
- Metal patterns for high-volume production
- Plastic and resin for detailed investment casting designs
Pattern Design Considerations
When making patterns, engineers must think about several things:
- Dimensional accuracy
- Surface finish needs
- Complex shapes
- Pattern strength
Shrinkage Allowance and Draft Angles
Knowing about metal shrinkage is crucial in pattern design. Shrinkage allowance helps with metal cooling shrink. Draft angles are also key, making it easy to remove the pattern without harming the casting.
Precision in pattern design leads to better casting quality and less need for post-processing.
Sand Casting Techniques and Mold Preparation
Sand casting is a key metalworking method. It turns raw materials into detailed metal parts. This method is great for making complex shapes with high precision and speed.
Sand Types and Selection
The first step in sand casting is picking the right sand mix. Experts use special sand mixes for making molds:
- Green sand: Moisture-based mixture most commonly used
- Ceramic sand: Provides enhanced heat resistance
- Synthetic sand: Offers consistent performance
Mold Preparation Process
Mold preparation is very detailed. Experts build sand molds by packing sand around detailed patterns. This ensures the metal is accurately cast and reduces defects.
Precision in sand casting begins with understanding material properties and mastering mold preparation techniques.
Investment Casting and Lost Foam Methods
Metal casting techniques are getting better, with investment casting and lost foam casting leading the way. These methods are great for making complex metal parts with high precision.
Investment Casting Process
Investment casting is a top-notch technique for making detailed metal parts. It involves several important steps:
- Creating a detailed wax pattern
- Developing a ceramic shell around the pattern
- Melting and removing the original wax model
- Pouring molten metal into the ceramic mold
- Breaking away the ceramic shell after solidification
Lost Foam Casting Applications
Lost foam casting is a new way to make complex metal parts. It uses foam patterns that melt away when metal is poured. The automotive and aerospace industries often use it for parts that are hard to make with traditional methods.
Die Casting and Permanent Mold Processes
Die casting and permanent mold casting are advanced ways to make metal parts. They are key in creating high-quality metal components for many industries.
Die Casting Advantages
Die casting uses high pressure to pour molten metal into metal dies. This method makes parts very accurate and smooth:
- Enables rapid production of intricate metal components
- Provides excellent dimensional tolerance
- Reduces post-production machining requirements
Permanent Mold Casting Steps
Permanent mold casting uses gravity or low-pressure to fill metal molds:
- Select appropriate metal alloy
- Prepare permanent metal mold
- Pour molten metal into mold
- Allow controlled cooling
- Remove finished component
Advanced metal casting techniques continue to revolutionize manufacturing precision and efficiency.
Pouring and Solidification Techniques
Metal casting needs careful control in the pouring and solidification stages. Techniques like squeeze casting and vacuum casting have changed the game.
Temperature Control Methods
Keeping the right temperature is key in metal casting:
- Maintain precise metal temperature
- Monitor thermal gradients
- Use specialized temperature measurement tools
Timing and Flow Rate Management
Vacuum casting gives great control over metal flow and solidification:
- Calculate optimal pouring speed
- Minimize turbulence during filling
- Ensure consistent metal distribution
Common Defect Prevention
Using advanced techniques like squeeze casting can greatly reduce defects:
- Identify potential casting defects early
- Use predictive modeling techniques
- Implement rigorous quality control processes
Post-Casting Operations and Surface Finishing
The metal casting process goes beyond just making the initial shape. It needs important steps after casting to make the parts precise and ready for use.
Cleaning and Preparation
Cleaning is the first big step after casting:
- Sandblasting for surface preparation
- Chemical cleaning for residue removal
- Mechanical tools for precision finishing
Quality Control Measures
Quality checks ensure metal integrity:
- Ultrasonic testing for internal defects
- X-ray scanning for hidden flaws
- Dimensional accuracy verification
Final Surface Treatments
Surface treatments enhance functionality:
- Painting for corrosion protection
- Plating for improved conductivity
- Special coatings for specific applications
The care taken in these steps is what makes metal parts work well and last long in many industries.
Ready to Transform Your Manufacturing?
Discover how our advanced steel casting technology can revolutionize your manufacturing process.
Contact Us Today